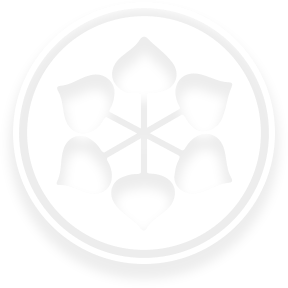
The future is design
TECHNOLOGY AT ITS BEST. STEP INTO THE FUTURE WITH OUR EXPERTISE.
Insights: S. Krishnakumar
Managing Director & CEO
At SPR, we have always focused on innovations, on improvisation of our products and services every day for which we completely rely on modern technology. We see it as a route map to growth for us as well as for all connected to us. By adopting modern technologies, we keep on doing business right for benefitting our stakeholders, strengthening relationships with partners, upskilling employees for better opportunities and giving back to the society that plays a major role in keeping us going through every thick and thin.
Tech Center
Situated at Ghaziabad, SPR Tech Centre is recognized by Department of Scientific and Industrial Research (DSIR), Government of India.
This is a state-of-the-art facility that provides a wide range of services for product design and development. We have a team of seasoned engineers and designers who can help with every aspect of the product development process, from initial concept to final production. We also have a wide range of equipment and resources to help you create a product that is duly validated virtually as well as physically.
Tech Centre at SPR is fully equipped to provide complete and comprehensive solutions, catering to the exacting needs of the hi-tech, new generation engines.
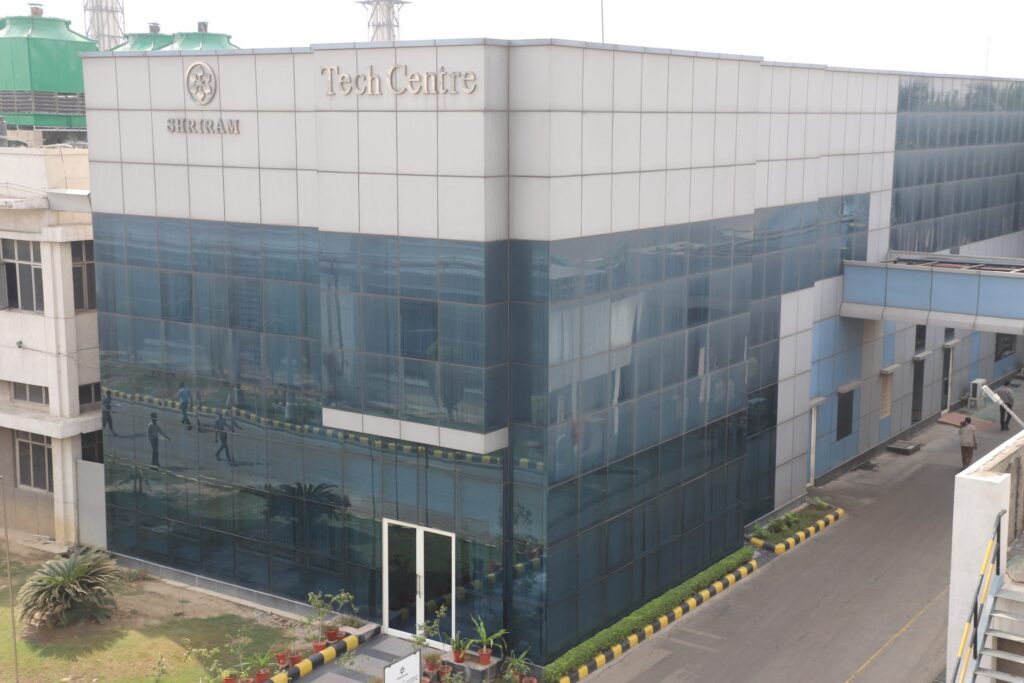
Our team of passionate engineers and designers are dedicated to creating products that meet the functional & fitment requirements of our esteemed customers. We work with our clients to understand their needs and then develop products that meet those needs employing modern generation resources including 3D modelling software, 3D scanner, Benchmarking data, design calculation and various optimization tools etc.
Tech Centre has an independent analysis lab for both metallurgical and meteorological analysis of tested samples. Facility is equipped with Scanning Electron Microscope, Confocal LASER scanning Microscope, X-ray Fluoresce system, Mahr Roundness Tester, Cylinder bore wear measurement system etc.
Tech Centre has advanced capabilities for simulation analysis of all portfolio products i.e. Pistons, Rings, and Engine Valves. Our in-house customized set of tools enable us to validate and optimize the design concepts and create design that are first time right.
Casting simulation through MAGMA software helps us to simulate casting process. We can do solidification analysis, filling analysis and velocity analysis etc to eradicate any possibility of casting defects.
The Piston concept model is refined through Finite Element Analysis (FEA) by applying the engine loading conditions. FEA analysis of a piston will yield following:
– Measurement of Side Forces and Wear pattern on the skirt
– Temperature Distribution across the entire cross-section
– Visualization of thermal and thermo-mechanical deformations
– Contact pressures on the skirt and pin bore
Factors of Safety at various zones of piston
Advance Piston Dynamic Analysis (SMA) is vital in understanding of the frictional behavior of the piston assembly as the frictional losses of the piston. Some factors that are considered when analyzing the secondary movement of a piston are Piston skirt deformation, Hydrodynamic lubrication, and Clearance in the connecting bearings etc.
One of the most popular Ring Dynamic Simulation software (RINGPACK), is used for estimation of:
– Gas blow-by and blow-back
– Oil consumption
– Friction and power losses and
– Wear rates for the ring faces, groove-ring side faces and liner.
Engine valve FEA enables us to simulate the design against combustion thermal load and mechanical loading created by Peak Cylinder Pressure.
State-of-the-art Rig Testing equipment is deployed for validating the prototype in a near virtual engine condition. For example, a Piston can be pulsated for over 2 million cycles to confirm the design strength under varying gas force loads. For an ultra light gasoline piston, the same test can be done to check fatigue failures both under gas forces and inertia forces.
Apart from these, there are custom made rigs for testing new materials and surface coatings in Piston Rings as well.
A dedicated engine testing facility has been established to validate the prototypes in line with the test cycles specified by the OEM. SPR is proud to have partnered with many leading OEMs for sharing the responsibility of testing for many new programs.
Engine testing facility is equipped with latest state-of-the-art facilities and capabilities like transient dynamometer for advanced engine test cycles, telemetry measurements etc.
The various tests being conducted are:
- Performance Testing
- Endurance Testing
- Cold & Hot Scuff Testing
- Micro-welding Testing
- Temperature Measurements on Pistons etc
A separate prototype cell is created for piston casting as well as piston machining with intent to produce prototype parts with minimum lead times for our customers. Prototype machining cell is equipped with sophisticated SPMs to be able to produce parts with various machining features.
Proto parts can also be produced from pre-cast billets for shorter lead times based on requirement of our esteemed customers.
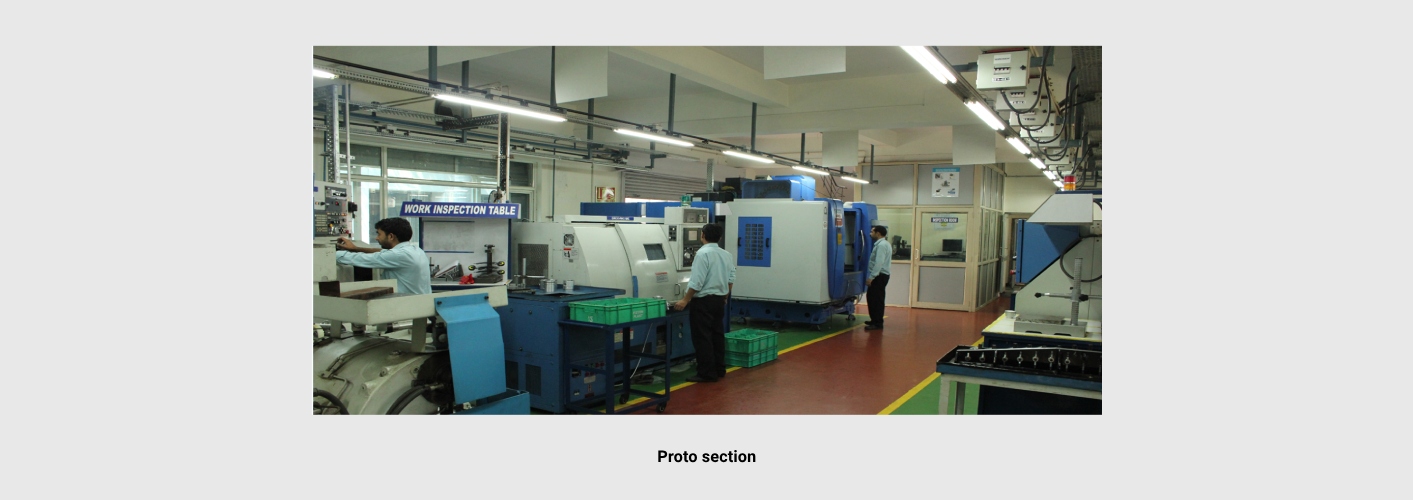
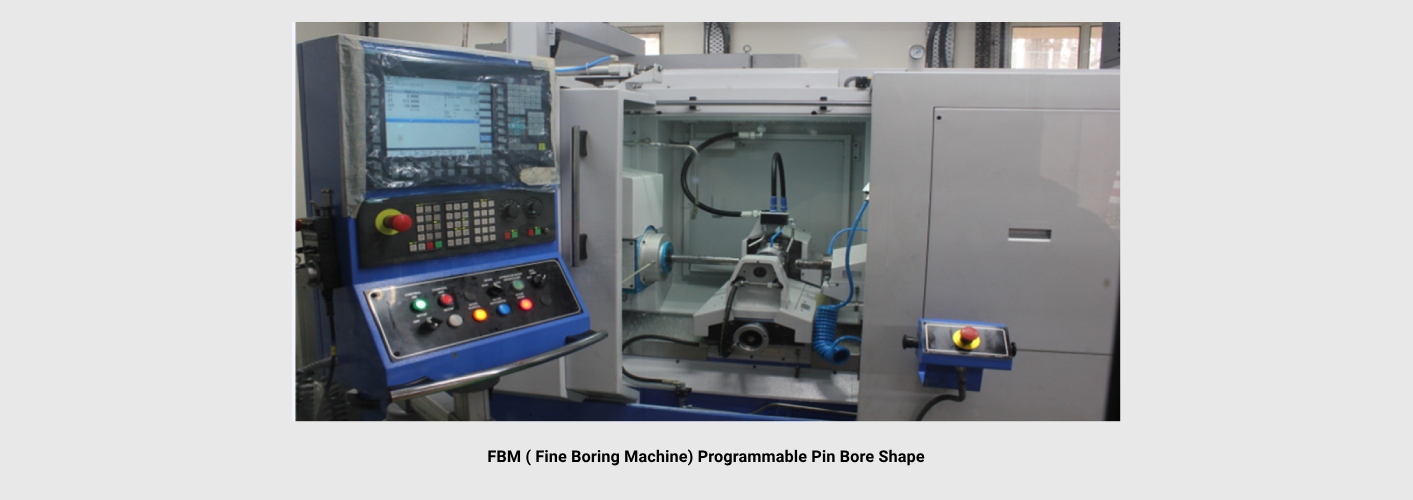
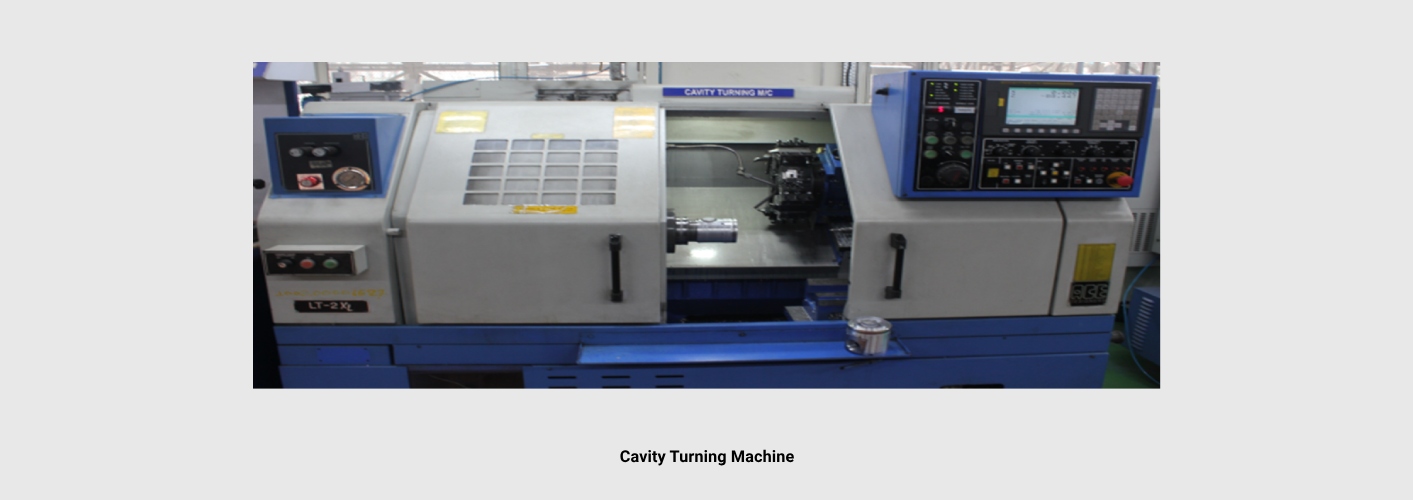
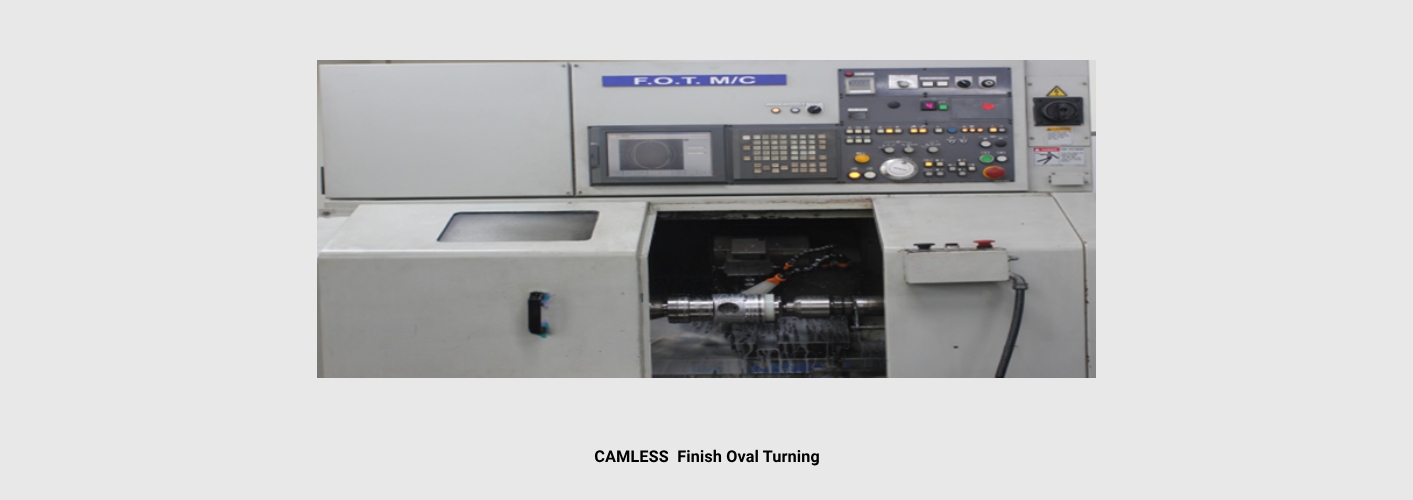
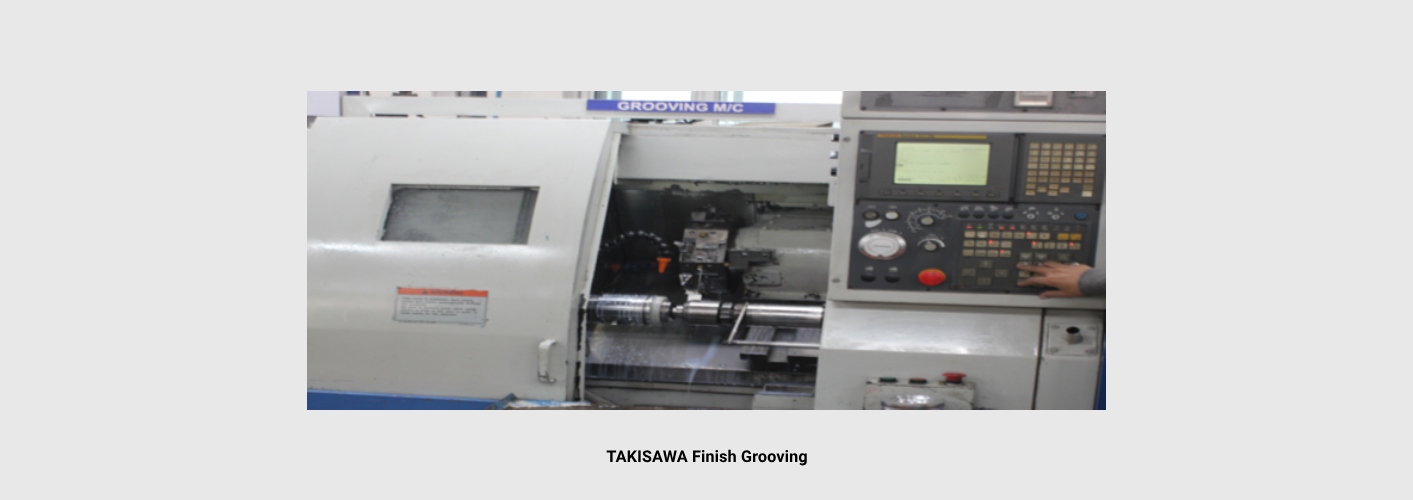
The concept model is refined through Finite Element Analysis (FEA) by applying the various load conditions foreseen in the engine. FEA analysis of a piston will yield following:
- Visualization of thermal and thermo-mechanical deformations
- Measurement of Side Forces and Wear pattern on the skirt
- Contact pressures on the skirt and pinbore
- Temperature Distribution across the entire cross-section
- Factors of Safety across the entire cross-section